The Clarinet BBoard
|
Author: vljenewein
Date: 2012-08-04 20:52
Just a thought. I can make duduks on my wood lathe, and see no problems in making clarinet barres on the lathe as well. I have some Ebony I am going to turn for a duduk, and was wondering if it would be good for a clarinet barrel? How about Apricot wood, or what about black cherry or pear? Most types of wood are available either at Woodcraft or on some online auctions. Most are just a few dollars in a blank. It takes me about 3 hours to turn an apricot square blank into a 13.3" duduk with an internal bore of 11.5mm and with finger-holes drilled on both sides. I think making a clarinet barrel would be a breeze.
Vern
Vernon
Jenewein Duduks Manufacturing & Research
www.duduk.us American made Duduks
|
|
Reply To Message
|
|
Author: vljenewein
Date: 2012-08-06 06:17
Well, I have a positive mental attitude. Once I have decent dimensions I can mimic that dimension in wood. The force is stong in my family. Recently I got a "vinage" clarinet on an ebay auction that was pretty much stuck together. Got it loose finally, and the whole thing is wood, ebony, with brass keywork. Not a sign one of serial number or who made it. The barrel is black and beautiful wood. I turned it so that it would take regular mouthpieces and regular upper joints/tenons and my wife commented to me how much difference it makes when I play it compared to the plastic barrel I have with this one Leblanc clarinet. It's dimensions should do. I anticipate the first one to be very good, and the rest to be excellent.
Vernon
Jenewein Duduks Manufacturing & Research
www.duduk.us American made Duduks
|
|
Reply To Message
|
|
Author: Bob Phillips
Date: 2012-08-10 16:44
Vernon,
A local acquaintance found that his specialized business of turning (two story tall) architectural columns was suffering in our housing recession. In an attempt to recover the lost income, he turned (no pun!) to his smaller lathes and started cranking out clarinet tuning barrels.
In one day I went through 2 grocery bags (about 140 barrels), mostly cocobollo, testing for responsiveness and tone quality. I found that 5% (7) of them were quite good --as far as my testing went. I bought two and had colleagues help me select from a pool of five --including two Buffets and a Tapliin-Weir.
The new guy's barrels won based strictly on listing to tone quality.
When played in earnest, however, the new barrels suffered such wide twelfths that they were useless.
I think that part of the problem was that their bores were improperly formed. I could not talk the lathe-man into reaming his barrel bores with taper.
Another quality issue involves getting the sockets on the same axis as the bore. If that's not the case, all bets are off! One place where this offset bore problem is evident is when you rotate the barrel a 1/4 turn at a time and find a "sweet spot" where it plays better. This can also happen when the unequal expansion along the flat grain and edge grain causes the barrel to go oval.
Oh, and another observation: all those barrel changes (with rough socket wall finishes) wore the cork off of my upper joint.
Mark is right. Good custom barrels are NOT something that you make with casual tooling.
Bob Phillips
|
|
Reply To Message
|
|
Author: vljenewein
Date: 2012-08-11 01:11
I'll take your advice, Bob.
On a Duduk I make the proximal end, the end that takes the reed mouthpiece is tapered. I have been able to solve that problem. I also have a reamer with a very slight taper to it. Now I know that I cannot begin to match the likes of the great barrel makers, but each tidbit of informaion, to help to "make" it better helps.
Turning wood is usually quarter sawn and once in a while you'll find pieces that are right at the center of the heart wood of the tree. These are few as many other blanks are made from thoses that have grain radiating around the heart wood. How you drill a hole for a Duduk is also important, since you want to drill perpendicular to the grain, and not with the grain if you can help it.
Do you have an idea on the amount of taper? I recenly received a small block of African Blackwood to try making a clarinet barrel out of. .. or 2.
I agree, the inside of the barrel needs to be glass smooth so that you can easily attach and take apart and not scuff up your cork.
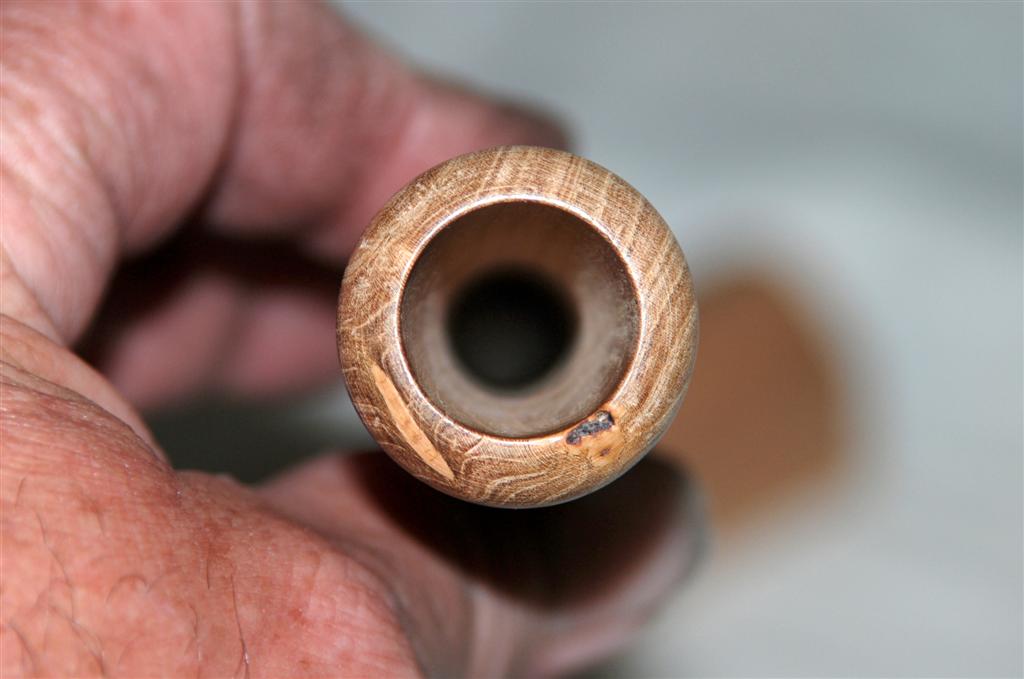
Picure of the end of Duduk #4 that I made. I can be seen the taper in this photo. This is of well aged apricot wood and is before lime treatment and treating with 100% pure Almond Oil.
This is the same mouthpiece after the treatment. Didn't notice the cloth artifact and other(s) at the time of taking the picture. I like the left over "knot" that lends character to this end of the Duduk.
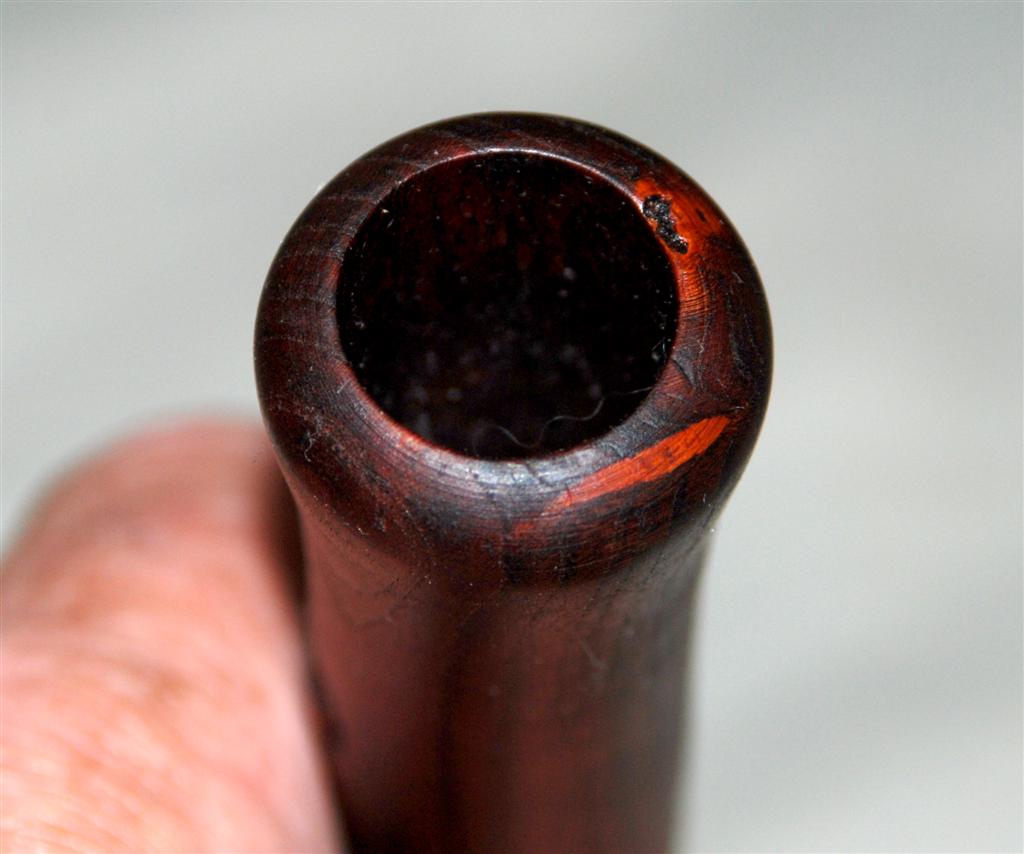
Vernon
Jenewein Duduks Manufacturing & Research
www.duduk.us American made Duduks
|
|
Reply To Message
|
|
Author: Garth Libre
Date: 2012-08-11 02:31
Well, whatever barrels and Duduks you are making and whatever success you are having with those new barrel experiments, I'm sure the results are pretty to look at. With those strong open grained woods, the results you get are beautiful. The one thing I don't like about grenadilla is that the grain is so tight the look is almost like brushed plastic from a distance. Keep us posted on your progress making barrels. Right now I'm getting ready to fix that Buffet barrel and to find a shorter 65 mm barrel that brings my pitch up a shade.
Garth
Garth, 305-981-4705. garthlibre@yahoo.com
|
|
Reply To Message
|
|
Author: Bob Phillips
Date: 2012-08-12 16:26
Tom Ridenour has a series of videos on youTube about clarinets. A couple of those deal with tapering of tuning barrel bores. In a story there, he tells of how he discovered that a common machinists' Morse Taper Reamer matched the taper in early Moening barrels.
It appears that (at least at the start) any old taper from a handy commercial tool sufficed.
I know that makers may use two different tapers --say steeply tapered at the top and a shallower taper at the bottom.
Bob Phillips
|
|
Reply To Message
|
|
Author: vljenewein
Date: 2012-08-12 17:02
Interesting. If you notice that taper on the pictures, it is done with one of my Morse Taper reamers. It matched the concert class Duduk made by well respected Armenian Master, Karen Mukayelyan exactly. I don't know if you have ever looked at how a Duduk is made but in Armenia they use some rather odd equipment, rather antiquated in a way, to produce Duduks that are used in concerts. Master Simon Duduk Making ... for what it's worth if your interested. Duduks are a long story....
Being steeply tapered at the top and shallower taper at the bottom would make sense. They are tapered from the mouthpiece end downward then. Is this correct?
Appreciate the info Bob!!
Vernon
Jenewein Duduks Manufacturing & Research
www.duduk.us American made Duduks
|
|
Reply To Message
|
|
The Clarinet Pages
|
 |